Are leaner business models endangering resilience?
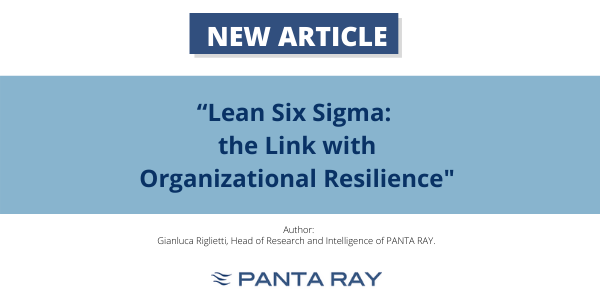
Modern organizations often develop business models that aim to eliminate superfluous efforts in their daily operations. It is important to maximize the results using the right amount of resources, balancing investments and returns. This is most evident in supply chain management, where methods such as lean manufacturing, often referred to just as “lean”, have become increasingly popular in recent years. Lean rests upon the idea that the supply process should optimize times both in terms of production and response to customers. In addition, only those goods that are strictly necessary to the production circulate in the supply chain, making timing and correct forecasting two key factors. This model dates back to the 1930s, when Toyota elaborated this production system that went on to become extremely popular.
On a similar note, an interesting perspective comes from the Six Sigma way, which consists in reducing variability as much as possible in the production process. The core concept is that a process should mirror certain optimal specificities in a consistent way, reducing unpredictability and establishing control over operations. The expression “Six Sigma” refers to a statistical variation, but it is more of a symbolic value when it comes to business application. Perhaps the best way to explain Six Sigma is through a real-life case mentioned in a paper by Christopher and Rutherford (2004):
In one Six Sigma project, Ford analysts measured inventory levels at one of their plants during production hours and found that levels varied by 20% over a month. With further investigation they discovered one of the major causes of inventory fluctuation was inefficient and inconsistent unloading of parts at the plant docks. Taking steps to improve dock utilisation and thus driving out process variability led to annual savings of more than $3.7 million due to inventory reduction, reduced overtime for unscheduled materials handling and other savings.
Some organizations recognize the value in both these approaches and have decided to merge the two, obtaining multiple benefits. While lean reduces waste in the whole process, Six Sigma helps standardise the process and avoid delays and inefficiencies in the delivery of goods and services. In fast and highly competitive markets this can become a significant advantage over other organizations, which is cost saving and it also maximizes efforts.
On the flip side, both approaches tend to eliminate redundancies in their effort to drive efficiency to its highest levels. It is worth wondering about the ability of such processes to withstand those disruptions that can still happen. Some have suggested to integrate lean and Six Sigma with some resilience measures, avoiding the risk to “lean down too far”. In this scenario, the organization reinvests part of the financial gains in risk mitigation and business continuity arrangements, allowing for some redundancy while also building a leaner production process.
Furthermore, a lean Six Sigma approach already embeds some resilience qualities in the organization. For instance, customer loyalty is likely to increase as a result of a faster and more efficient process, due to better time management and strategic planning. On a similar note, reducing variations in operational processes helps avoid several small daily disruptions that can take a significant toll in the long term. For instance, according to the BCI Horizon Scan, in 2019 health and safety incidents were among the costliest types of disruptions, more than cyber-attacks.
Thus, while there is obviously a trade-off between leaner management systems and resilience approaches that aim to build redundancy in case of disruptions, the two are not mutually exclusive. With the right integration, they can actually become complementary. However, it is important not to prioritize being faster over being resilient. If the past 24 months have taught us anything, it is that uncertainty is not the exception but the norm. Therefore, sustainable, modern organizations must build resilience qualities as a strategic goal, not as a nice-to-have.
A Forbes article presents an interesting metaphor between organizations and the human body on the topic:
This is why our body has built in so many “redundancies.” We have two arms, two legs, two lungs, two kidneys, two eyes and two ears. And we have tremendous over-capacity in our brain, our muscles, our bones, our fat, our lungs, our blood, and more. Efficiency-wise this might be superfluous and if we were managing our body in the same way as we are managing our organizations, all of that were long gone.
But there is a reason for all this redundancy. It makes us resilient. Or, as Nassim Nicholas Taleb calls it, it makes us antifragile. Given that our species already survives and thrives a bit longer than there are organizations, a focus on resilience seems to be the better choice in the long-run.
The point of this discussion is to demonstrate that resilience functions such as enterprise risk management and business continuity management are indeed compatible with business attitudes that aim to build competitive advantage. Organizations should not have to choose between being efficient and being secure; hence, changing the narrative on the matter can go a long way in changing top management’s perspective on the subject.
To conclude, below you can find a list of activities typical of a business continuity management system that can actually boost productivity and efficiency in the organization:
- The Business Impact Analysis (BIA). This consists of an analysis of all the internal and external interdependencies of an organization, which allows to build a comprehensive mapping of your operations. The output can help identify those functions or suppliers that need strengthening, while also providing management with a clearer idea of the value each function produces;
- Crisis simulations. These are tests that an organization can carry out to test its ability to withstand a disruption, it shows where things could go wrong in the case of a real-life disruption and it helps stabilize internal and external processes;
- Embedding. This is a key activity in business continuity management and its purpose is to engage key figures such as top management and process owners in the resilience-building process. It also has the advantage of building better communications channels that can take down organizational silos and increase collaboration;
- Horizon scanning. This task has the primary goal of scanning for risks and opportunities in the medium and long term. Both lean and six sigma rely significantly on correct forecasting and can therefore benefit from the output of this type of analysis.