Can a lean methodology ensure Resilience for organizations?
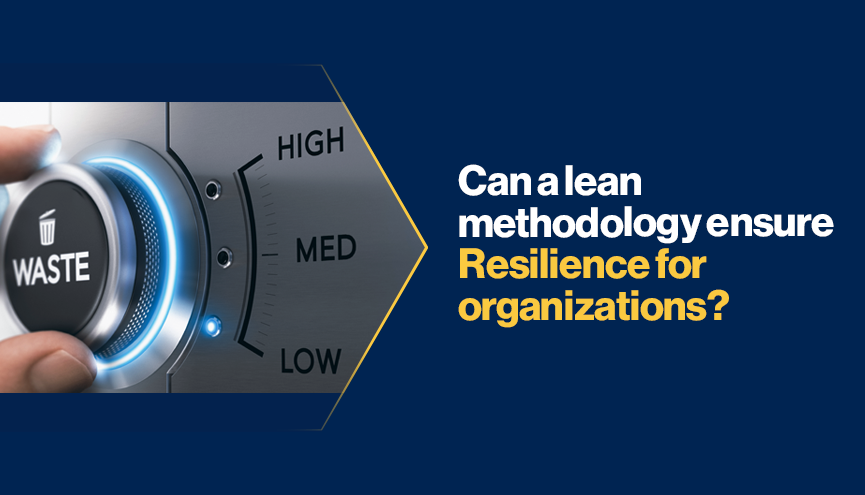
The main challenge of lean management is the reduction (or removal) of waste, creating methods and standardizing processes, while increasing organizational efficiency by focusing decisions and management on continuous improvement and growth.
According to lean methodology, by reducing and eliminating unnecessary processes or steps you can ensure that customers are getting what they want while reducing the cost of producing that product or service at the same time.
It is not just an applicable work methodology, but it can also generate other kinds of benefits for the organization, such as the introduction of a new mindset, culture and principals which are aimed towards innovation and a high level of problem solving capabilities.
The five principles of Lean, according to Womack and Jones:
Define the value: quantify and clarify what the customer is willing to pay for.
Map the value stream: using the customer’s values as a reference point, all the activities that contribute to these values are identified. The remaining ones, which do not add value to the end customer, are considered waste and are classifiable in two categories: non-valued added but necessary (reducible as much as possible) and non-value added & unnecessary (pure waste, can be cut). Actually, in the organization, wastes can be classified through the 7W+1 system:
- product or service defects that fail to meet customer expectations
- overproduction, causing supply to exceed demand
- time spent waiting for the next process step
- time spent in unnecessary transportation of products and materials
- unprocessed materials expiring while still in inventory
- the unnecessary movement of people
- extra-processing of the product beyond what is necessary to meet the quality standards
+1) unused talent, as people’s skills and knowledge are consistently underutilized.
Create flow
Design a new sustainable flow of the valuable activities without interruptions or delays, ensuring that value-adding activities flow smoothly. The organization can adopt strategies like re-configuring the production steps, leveling out the workload, creating cross-functional departments, and training employees to be multi-skilled and adaptive.
Establish pull
The goal of a pull-based system is to speed up and mold the flow based on the needs of the end customers, while ensuring that the requisite materials and information are available for just-in-time delivery and manufacturing, where products are created at the time and quantity required.
Pursue perfection
Considered the most fundamental principle among them all, affecting the organizational culture and introducing lean thinking and continuous process improvement - where every employee should strive towards perfection, thereby standardizing the achieved level, and find ways to get a little better every day.
The benefits of lean
The more common benefits of the lean implementation can be recognised as, but not limited to:
- increase of effectiveness in processes and in terms of quality in achieving the final objectives
- greater qualitative focus on activities with greater added value
- development of individual skills and resource empowerment
- continuous improvement of the product or service offered, thanks to attention on the customer's objectives
- increase in the perceived value of the product or service.
Can lean methodology ensure Resilience in an organization?
Clearly the answer is no, but neither we can consider lean efficiency to be opposed to resiliency.
Although lean manufacturing is highly efficient at the best of times, it’s also highly susceptible to disruption in the worst, with operational flexibility considered to be a required step.
For manufacturers to effectively combine efficiency and resilience, factors such as monitoring valuable and reliable data to reduce or completely avoid disruptions to their manufacturing processes, as well as knowledge and understanding of what their supply chains look like at any given moment, can make the difference.
Companies can achieve an effective combination with important elements like:
- Total visibility into financial and operational flexibility
- Health and just in time monitoring in all factories
- Continuous operation through a connected worker platform.
Lean methodology can also efficiently support organizations in their worst-case scenarios through the mindset that it introduces, regarding the minimization of waste in the process, the high capability of its people to problem solve, the application of PDCA, and near-miss and ‘What if’ scenario analysis methodologies to anticipate the introduction of needed actions to success.